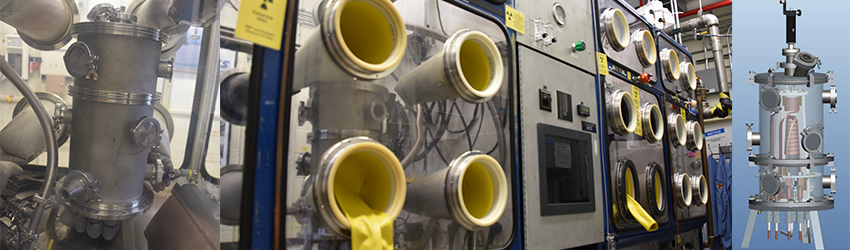
Instrument Description
The glovebox advance casting system (GACS) furnace is located inside the casting laboratory glovebox, which is an inert atmosphere. The casting operations will primarily involve uranium and plutonium in quantities nominally around 300 g total alloy weight. A typical charge composition based on weight percent of alloying agent might look like U-10Zr, U-20Pu-10Zr, or U-20Pu-10Zr-2Np-3Am. Additional alloying agents, to include molybdenum, may be used as well as varying compositions that may include or not include radiological materials.
The GACS is a system composed of a specially designed furnace enclosed in a stainless-steel enclosure that houses structures to accommodate a mold(s), crucible, induction coils, thermocouples, and secondary containment to capture melt upon failure of other internal components. The molds and crucible are made of graphite, but different materials may be tested in the future and are included as part of the scope for this LI. The induction-heated crucible is sized for approximately 500 grams of uranium alloy. A typical charge will be 300 grams or less of total material.
The furnace orientation is configured vertically with the crucible positioned directly above the mold. The furnace enclosure is a multipiece stainless-steel chamber composed of a base, two cylindrical sections, and a lid. GACS, which does not require reduced pressures for casting, reduces high-level waste production, and increases overall casting efficiency by reducing the size of the recycle stream. As part of this effort, the GACS was developed and installed in a plutonium-qualified glovebox.
The furnace has an administrative control of 1,650°C on the operating temperature, which is controlled through a subroutine not routinely accessed during run programming, and intended to protect against failure of a ceramic sleeve surrounding the crucible. This added safety feature precludes inadvertent change of the maximum operating temperature. This control is set 50° below the maximum operating temperature of the sleeve and 150° below its failure temperature. Routine operating temperatures will typically be at 1,500°C or lower.
The furnace is operated with the melt under inert gas cover or a vacuum. The inert gases are delivered to the furnace from either compressed gas cylinders or building supply. If counter gravity injection casting is performed, an accumulator tank may be used, the accumulator pressure will be administratively controlled to 15 psig and a pressure relief valve will be installed to ensure pressure remains below approximately 17 psig. The chamber pressures will be administratively controlled to 12 psig or less.
Applications
The Fuel Cycle Research and Development (FCRD) program developed the GACS, which does not require reduced pressures for casting, reduces high-level waste production, and increases overall casting efficiency by reducing the size of the recycle stream. As part of this effort, the GACS was developed and installed in a plutonium–qualified glovebox. As a precursor to this activity a bench-scale casting system (BCS) was fabricated and installed in a radiological hood. This system was used to cast numerous uranium-based pins and was the basis for the GACS design.
Specifications
A typical charge will be 300 grams or less of total material.
Routine operating temperatures will typically be at 1,500°C or lower.
Accumulator pressure will be administratively controlled to 15 psig.
Chamber pressures will be administratively controlled to 12 psig or less.